塑膠專欄
智慧型輕質材料之發展與應用
智能材料
智慧型輕質材料之發展與應用
塑膠中心 張凱捷 博士
摘要
在3C消費性電子產品、交通運輸車輛、建築裝潢材料、紡織皮革材料及醫療產品等各項重要產業之中,往往因為產品訴求的功能與應用不同,對應的界面處裡技術亦需求不同;其中界面修復技術則建立在材料具有薄膜特性,對於各個產品提供複合保護層,對於抗刮表面,須提供硬質自我修復材料,對於延展表面,則須提供彈性自我修復材料,無論何種界面修復需求,解決表面層及接著層之裂痕自我修復之需求為未來市場趨勢,面對高階界面處理材料多數為仰賴國外進口,除了成本價格高,因應各產業需求技術變化少,為滿足各式產品應用上,以國內上游化學材料,建立高階界面處理材料,提供各種產品智能界面處理材料,補足產業主要技術缺口。
前言
延續過去塑膠中心智能材料技術開發,逐步建構智能材料技術平台,優先透過材料界面黏滯特性的控制技術解決產業界所面臨之界面貼合問題,並規劃熱能、光能與機械能等能量方式建構完整刺激源設計智能材料。藉由光/熱刺激響應特性基礎概念進行刺激源多元化,更廣泛延伸至其他本質性應力刺激響應材料的機理發展,建立以氫鍵作用力為主力的自修復行為,應用在四種民生泛用材料(鋁合金、塑膠、木材、皮革)上;此外,更進一步考量後端應力刺激響應材料的市場開發及使用,發展纖維複合材料系統上之刺激響應材料,針對纖維複合材料之樹脂進行開發,強化刺激響應產品可運用之範圍;透過材料的特性提升及不同的加工運用,進行塑膠材料不同領域的開發與應用,解決應力所產生出裂紋,無論為異質表面受損或同質內部危害,都能達到95%以上回復狀況不會立即造成損害,有效地透過修復材料的控制,為刺激響應材料提供更廣的產品設計及應用範疇。
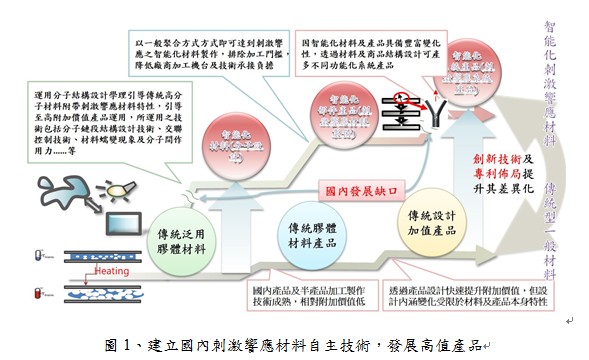
皮革、自行車及塑膠件外觀保護材料主要以塗料及烤漆進行塗裝,但目前自我修復材料,除了進口價格昂貴外,國內自我修復材料技術僅有工研院NIPU材料,進行外觀保護材料,與國外技術一致,利用材料的彈性,本技術將經由同質界面裂痕修復控制技術與異質界面表面處理控制技術,以自我修復膠體及複合板材為最終計畫目標載具,並進行配方設計及加工技術輔導國內產業以產出符合業界現階段使用之具市場競爭力及高值化產品。
為解決微結構裂紋引發結構安全性危害並提高高階技術產品之自主性,將透過具分子間吸引力材料修復應答控制技術進行相關技術之發展,並以應力刺激響應膠體及複材作為計畫目標載具進行配方設計以產生符合業界現階段使用之產品。
本質型自我修復材料開發技術
運用分子間吸引力設計材料高度內聚力特性,當材料受到外力或環境作用,材料表面或內部由彈性變形至塑性變形而開始形成微觀裂纹,在材料表面或內部裂纹擴展至斷裂之前,可依循裂紋尖端逐步往大裂痕方向自我修復,如同拉鍊般方式進行修復歷程。計畫中應力刺激響應修復材料開發為技術之重點,結合過去熱光刺激響應技術,並設計應力刺激誘發自我修復膠體在特定微結構裂痕範圍內進行裂痕界面自身反射修復行為,如聚醯烯胺系或聚醯胺等分子結構,大幅提升裂痕界面自我貼合能力,自我修復歷程與微觀修復基理(如圖2)。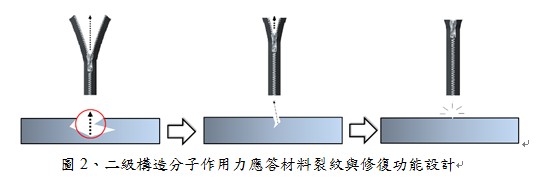
藉由設計氫鍵分子間吸引力、立體空間效應及烷鏈斷效應,運用分子結構不對稱特性,低玻璃轉化溫度的效果,避免高分子鏈結晶或束縛,控制分子量增加分子鏈運動之自由體積以達到材料內聚力可自我修復功能。
材料規格-自我修復材料合成
研究中以雙酸/三酸先與烯胺於高溫下進行反應得到前驅物,再與胺類化合物進行反應後得到最終成品,合成路徑如圖5所示。由FTIR實驗確認產品官能基訊號(圖6a),進一步判定峰值對應官能基:於1715 cm-1出現C=O鍵訊號峰;3286 cm-1出現N-H鍵訊號峰,可推測所合成之自我修復材料成品如預期設定為聚醯胺高分子。以GPC實驗分析產品分子量,由檢測數據圖譜分析(圖6b):產品Mw=91,858 g/mole,PD為1.48。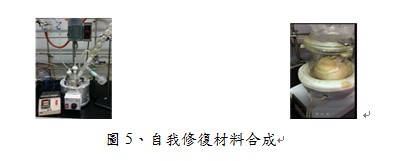
材料規格-自我修復能力驗證
拉力強度變化量進行材料自我修復率之評估方式,實驗規範以ASTM D638為基準。將材料壓製成啞鈴型標準試片,測得修復前的斷裂荷重數據均值為450±1 gf,將試片裁切後,並將試片接合修復後,測得修復後斷裂荷重數據均值為427±4 gf。比對計算成品之拉力強度回復率為95.1%。相關數據如表1所示,而相關實驗過程如圖7所示。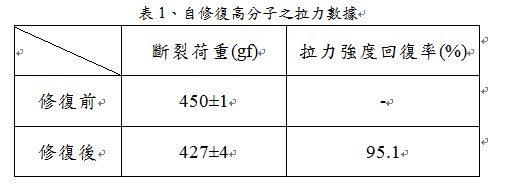
加工規格-溶劑系統規格驗證
經由溶解度實驗,了解自我修復產品於一般溶劑系統內溶解度差異性,利於後續開發各種加工製程應用,如噴塗、刮塗、含浸等,拓展自我修復產品應用民生消費性產業、3C產品殼件產業等表面自我修復層用途。此外,配合一般用於噴塗設備之塗料產品常規固型份約為40 %,因此實驗設計部份就配製成40 %溶液進行溶解度測試,實驗結果如表2、圖15所示。水性溶劑中,成品於水、丙酮、丁酮、乙酸乙酯、乙酸正丁酯等溶劑中不易溶解,而於乙醇及甲苯呈現澎潤現象,但可溶於異丙醇,及油性溶劑系統可溶於氯仿或醇類共溶劑。此階段實驗結果,未來以低voc溶劑異丙醇進行自我修復塗料產品物性調整,滿足塗料業綠色產品需求性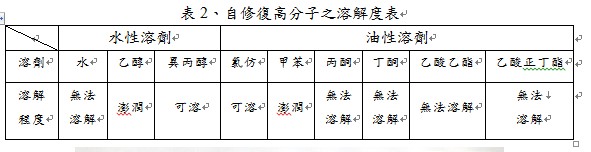
加工規格-加工製程規格確認
塗佈產業之噴塗製程則需具備高流動性塗料,黏度要求為200~1,000 cp,而刮塗製程所需黏度要求為2,000~5,000 cp。藉由調整溶劑劑量達到控制材料的黏度,找到較佳平衡點約為2,200 cp(如圖9所示)。同時顧慮到塗層太薄則塗料無法完全覆蓋於基材之疑慮;塗層太厚則會消耗過多的塗料使成本增加,目前塗層厚度於業界中對於刮塗製程的厚度為1~25μm,而噴塗製程厚度為25~60μm。本研究之刮塗厚度為20.01μm,噴塗厚度為31.22μm(如圖9b所示),可符合業界所需要求,於此厚度下仍具有表面自我修復特性,而膜材於0~80℃冷熱循環下,實驗測試均值93次以上,仍具自我修復特性。
應用規格-基材表面處理、硬度、密著性與耐溶劑性
(1)為拓展自我修復材料應用產業,選定四種基材:塑膠(極性表面ABS、TPU,非極性表面PP)、木材、皮革、鋁合金,初步選定表面積提升法(Sandpapering method)、表面能增加法(corona method)、表面能化學鍵結(primer),改善高分子基材表面能,並使用達因筆確認其數值。由於木材及鋁合金於使用電暈法前表面能已達48達因,所以無須進行電暈法前處理步驟。經電暈法進行表面改質,高分子基材表面能皆已達38達因以上(相關數據請參考表3所示)。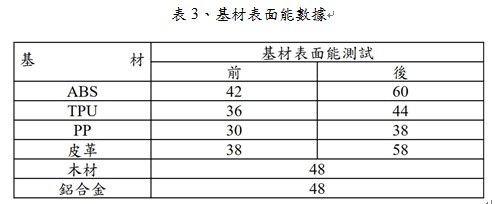
(2)將自我修復材料塗佈於表面改質基材,基材包含塑膠(極性表面ABS、TPU,非極性表面PP)、木材、皮革、鋁合金,經百格測試,測試規範為ASTM D3359,自我修復表層皆達4B以上(相關數據請參考表4所示)。
自我修復材料塗佈於表面改質基材,包含塑膠(極性表面ABS、TPU,非極性表面PP)、木材、皮革、鋁合金,經硬度測試,自我修復表層硬度皆達2H以上(相關數據請參考表10所示)。將自我修復材料塗佈於表面改質基材,包含塑膠(極性表面ABS、TPU,非極性表面PP)、木材、皮革、鋁合金,經百格測試自我修復表層皆達4B以上,顯示密著性優異;而表面塗層經耐溶劑實驗測試,外觀變化也皆無變化。
載具規格-載具密著性及耐溶劑測試
(1)載具部份選定自行車、紡織皮革、及行李箱進行自我修復材料應用測試。將自我修復材料塗於鋁合金自行車架、噴塗於皮革鞋材、及噴塗於ABS行李箱外殼,經ASTM D3359測試塗層與載具基材密著度,研究結果皆達4B以上(測試結果請參考圖10所示)。
(2)針對鋁合金自行車架擷取部分構件進行CNS 3883實驗,於:於5%鹽水、80℃、1小時測試後,經經測人員判定構件塗層並無外觀變化,通過耐鹽霧測試(測試結果請參考圖11a所示)。針對皮革鞋材擷取部分皮件進行AATCC NO.10水洗牢度實驗,獲得標準4.5,一般紡織業者需求標準約為3~4分即可通過,同時經檢測人員判定構件塗層並無外觀變化(測試結果請參考圖11b所示)。針對ABS行李箱擷取部分構件進行CNS 9199實驗,於5%鹽水、23℃經3小時測試,經檢測人員判定構件塗層並無外觀變化,通過耐鹽霧測試(測試結果請參考圖11所示)。
載具規格-裂紋修復微結構分析測試
藉由SEM觀察自我修復材料微觀裂紋恢復情況,製備寬度為寬度62.32μm的裂紋可於30分鐘內修復0.098μm,與計畫相符(測試結果請參考圖12所示)。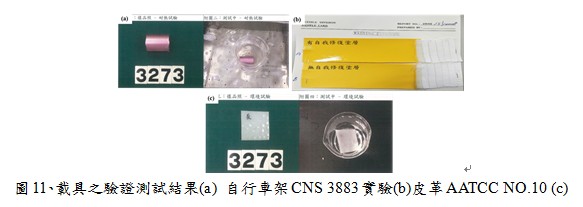
結論
為改變國內傳統業者面臨低價競爭之困境,塑膠中心運用自我修復高分子材料具表面與結構修復運用性廣泛之特點,進行以丙烯酸酯為主之自我修復材料開發,亦成功與業者共同開發出國內首批自製具有表面自我修復功能的自行車架、皮鞋與旅行箱等產品,除有效解決國內自我修復材料仰賴國外進口的問題,同時也將丙烯酸酯單體升級為民生用表面自我修復產品,運用價值大幅提升,由每公斤40元提高約10倍以上價格,擺脫國內業者過去丙烯酸酯材料低價競爭的現況,現在廠商已具備合成自我修復高分子材料之技術與能量,除了運用其特性將產品高值化之外,亦解決國內自我修復材料功能不一問題,並協助業者符合國際新材料發展需求及取得全球市場競爭利基。
塑膠中心 張凱捷 博士
摘要
在3C消費性電子產品、交通運輸車輛、建築裝潢材料、紡織皮革材料及醫療產品等各項重要產業之中,往往因為產品訴求的功能與應用不同,對應的界面處裡技術亦需求不同;其中界面修復技術則建立在材料具有薄膜特性,對於各個產品提供複合保護層,對於抗刮表面,須提供硬質自我修復材料,對於延展表面,則須提供彈性自我修復材料,無論何種界面修復需求,解決表面層及接著層之裂痕自我修復之需求為未來市場趨勢,面對高階界面處理材料多數為仰賴國外進口,除了成本價格高,因應各產業需求技術變化少,為滿足各式產品應用上,以國內上游化學材料,建立高階界面處理材料,提供各種產品智能界面處理材料,補足產業主要技術缺口。
前言
延續過去塑膠中心智能材料技術開發,逐步建構智能材料技術平台,優先透過材料界面黏滯特性的控制技術解決產業界所面臨之界面貼合問題,並規劃熱能、光能與機械能等能量方式建構完整刺激源設計智能材料。藉由光/熱刺激響應特性基礎概念進行刺激源多元化,更廣泛延伸至其他本質性應力刺激響應材料的機理發展,建立以氫鍵作用力為主力的自修復行為,應用在四種民生泛用材料(鋁合金、塑膠、木材、皮革)上;此外,更進一步考量後端應力刺激響應材料的市場開發及使用,發展纖維複合材料系統上之刺激響應材料,針對纖維複合材料之樹脂進行開發,強化刺激響應產品可運用之範圍;透過材料的特性提升及不同的加工運用,進行塑膠材料不同領域的開發與應用,解決應力所產生出裂紋,無論為異質表面受損或同質內部危害,都能達到95%以上回復狀況不會立即造成損害,有效地透過修復材料的控制,為刺激響應材料提供更廣的產品設計及應用範疇。
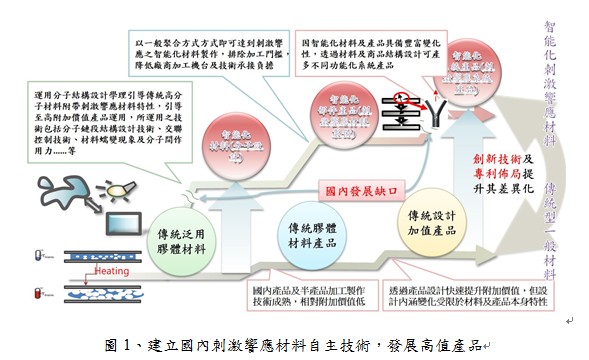
皮革、自行車及塑膠件外觀保護材料主要以塗料及烤漆進行塗裝,但目前自我修復材料,除了進口價格昂貴外,國內自我修復材料技術僅有工研院NIPU材料,進行外觀保護材料,與國外技術一致,利用材料的彈性,本技術將經由同質界面裂痕修復控制技術與異質界面表面處理控制技術,以自我修復膠體及複合板材為最終計畫目標載具,並進行配方設計及加工技術輔導國內產業以產出符合業界現階段使用之具市場競爭力及高值化產品。
為解決微結構裂紋引發結構安全性危害並提高高階技術產品之自主性,將透過具分子間吸引力材料修復應答控制技術進行相關技術之發展,並以應力刺激響應膠體及複材作為計畫目標載具進行配方設計以產生符合業界現階段使用之產品。
本質型自我修復材料開發技術
運用分子間吸引力設計材料高度內聚力特性,當材料受到外力或環境作用,材料表面或內部由彈性變形至塑性變形而開始形成微觀裂纹,在材料表面或內部裂纹擴展至斷裂之前,可依循裂紋尖端逐步往大裂痕方向自我修復,如同拉鍊般方式進行修復歷程。計畫中應力刺激響應修復材料開發為技術之重點,結合過去熱光刺激響應技術,並設計應力刺激誘發自我修復膠體在特定微結構裂痕範圍內進行裂痕界面自身反射修復行為,如聚醯烯胺系或聚醯胺等分子結構,大幅提升裂痕界面自我貼合能力,自我修復歷程與微觀修復基理(如圖2)。
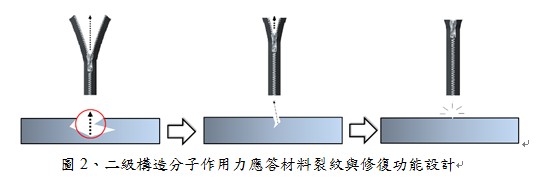
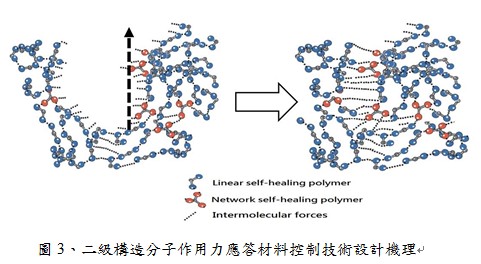
藉由設計氫鍵分子間吸引力、立體空間效應及烷鏈斷效應,運用分子結構不對稱特性,低玻璃轉化溫度的效果,避免高分子鏈結晶或束縛,控制分子量增加分子鏈運動之自由體積以達到材料內聚力可自我修復功能。
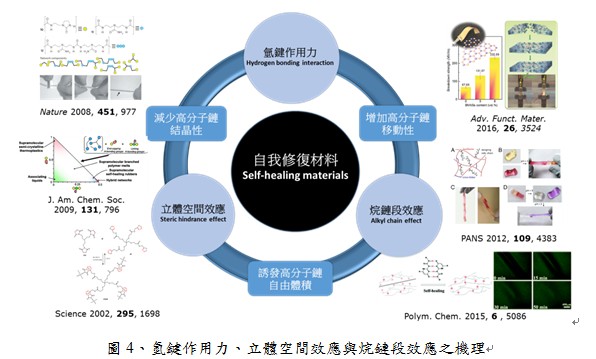
研究中以雙酸/三酸先與烯胺於高溫下進行反應得到前驅物,再與胺類化合物進行反應後得到最終成品,合成路徑如圖5所示。由FTIR實驗確認產品官能基訊號(圖6a),進一步判定峰值對應官能基:於1715 cm-1出現C=O鍵訊號峰;3286 cm-1出現N-H鍵訊號峰,可推測所合成之自我修復材料成品如預期設定為聚醯胺高分子。以GPC實驗分析產品分子量,由檢測數據圖譜分析(圖6b):產品Mw=91,858 g/mole,PD為1.48。
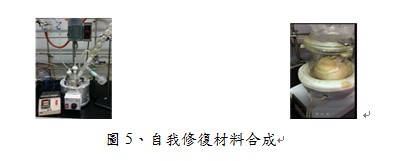
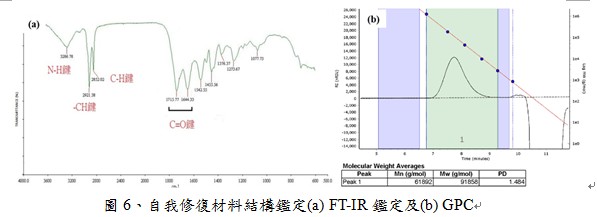
拉力強度變化量進行材料自我修復率之評估方式,實驗規範以ASTM D638為基準。將材料壓製成啞鈴型標準試片,測得修復前的斷裂荷重數據均值為450±1 gf,將試片裁切後,並將試片接合修復後,測得修復後斷裂荷重數據均值為427±4 gf。比對計算成品之拉力強度回復率為95.1%。相關數據如表1所示,而相關實驗過程如圖7所示。
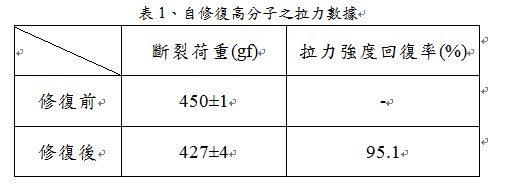
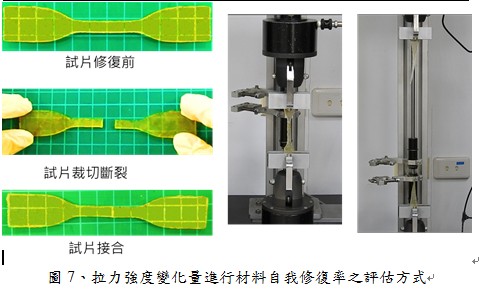
加工規格-溶劑系統規格驗證
經由溶解度實驗,了解自我修復產品於一般溶劑系統內溶解度差異性,利於後續開發各種加工製程應用,如噴塗、刮塗、含浸等,拓展自我修復產品應用民生消費性產業、3C產品殼件產業等表面自我修復層用途。此外,配合一般用於噴塗設備之塗料產品常規固型份約為40 %,因此實驗設計部份就配製成40 %溶液進行溶解度測試,實驗結果如表2、圖15所示。水性溶劑中,成品於水、丙酮、丁酮、乙酸乙酯、乙酸正丁酯等溶劑中不易溶解,而於乙醇及甲苯呈現澎潤現象,但可溶於異丙醇,及油性溶劑系統可溶於氯仿或醇類共溶劑。此階段實驗結果,未來以低voc溶劑異丙醇進行自我修復塗料產品物性調整,滿足塗料業綠色產品需求性
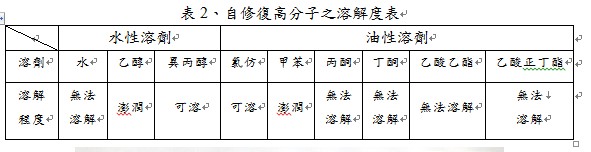
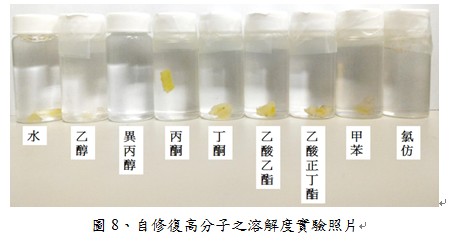
加工規格-加工製程規格確認
塗佈產業之噴塗製程則需具備高流動性塗料,黏度要求為200~1,000 cp,而刮塗製程所需黏度要求為2,000~5,000 cp。藉由調整溶劑劑量達到控制材料的黏度,找到較佳平衡點約為2,200 cp(如圖9所示)。同時顧慮到塗層太薄則塗料無法完全覆蓋於基材之疑慮;塗層太厚則會消耗過多的塗料使成本增加,目前塗層厚度於業界中對於刮塗製程的厚度為1~25μm,而噴塗製程厚度為25~60μm。本研究之刮塗厚度為20.01μm,噴塗厚度為31.22μm(如圖9b所示),可符合業界所需要求,於此厚度下仍具有表面自我修復特性,而膜材於0~80℃冷熱循環下,實驗測試均值93次以上,仍具自我修復特性。
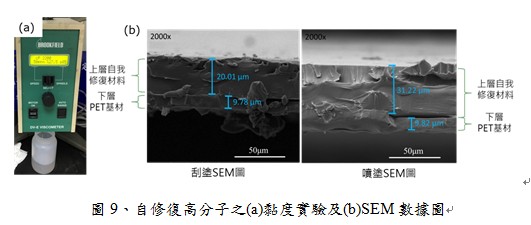
應用規格-基材表面處理、硬度、密著性與耐溶劑性
(1)為拓展自我修復材料應用產業,選定四種基材:塑膠(極性表面ABS、TPU,非極性表面PP)、木材、皮革、鋁合金,初步選定表面積提升法(Sandpapering method)、表面能增加法(corona method)、表面能化學鍵結(primer),改善高分子基材表面能,並使用達因筆確認其數值。由於木材及鋁合金於使用電暈法前表面能已達48達因,所以無須進行電暈法前處理步驟。經電暈法進行表面改質,高分子基材表面能皆已達38達因以上(相關數據請參考表3所示)。
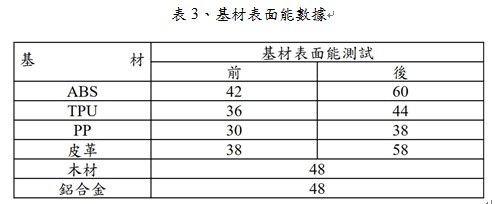
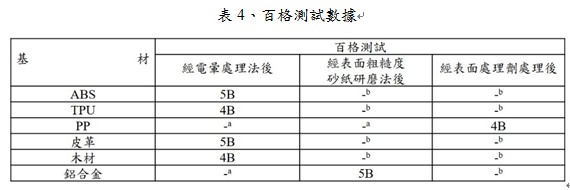
(2)將自我修復材料塗佈於表面改質基材,基材包含塑膠(極性表面ABS、TPU,非極性表面PP)、木材、皮革、鋁合金,經百格測試,測試規範為ASTM D3359,自我修復表層皆達4B以上(相關數據請參考表4所示)。
自我修復材料塗佈於表面改質基材,包含塑膠(極性表面ABS、TPU,非極性表面PP)、木材、皮革、鋁合金,經硬度測試,自我修復表層硬度皆達2H以上(相關數據請參考表10所示)。將自我修復材料塗佈於表面改質基材,包含塑膠(極性表面ABS、TPU,非極性表面PP)、木材、皮革、鋁合金,經百格測試自我修復表層皆達4B以上,顯示密著性優異;而表面塗層經耐溶劑實驗測試,外觀變化也皆無變化。
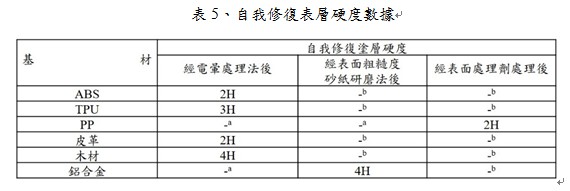
載具規格-載具密著性及耐溶劑測試
(1)載具部份選定自行車、紡織皮革、及行李箱進行自我修復材料應用測試。將自我修復材料塗於鋁合金自行車架、噴塗於皮革鞋材、及噴塗於ABS行李箱外殼,經ASTM D3359測試塗層與載具基材密著度,研究結果皆達4B以上(測試結果請參考圖10所示)。
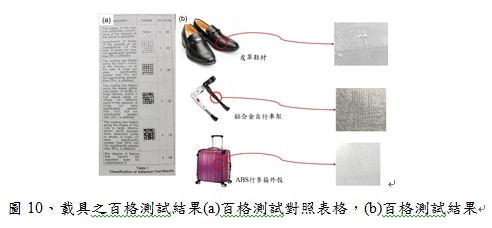
(2)針對鋁合金自行車架擷取部分構件進行CNS 3883實驗,於:於5%鹽水、80℃、1小時測試後,經經測人員判定構件塗層並無外觀變化,通過耐鹽霧測試(測試結果請參考圖11a所示)。針對皮革鞋材擷取部分皮件進行AATCC NO.10水洗牢度實驗,獲得標準4.5,一般紡織業者需求標準約為3~4分即可通過,同時經檢測人員判定構件塗層並無外觀變化(測試結果請參考圖11b所示)。針對ABS行李箱擷取部分構件進行CNS 9199實驗,於5%鹽水、23℃經3小時測試,經檢測人員判定構件塗層並無外觀變化,通過耐鹽霧測試(測試結果請參考圖11所示)。
載具規格-裂紋修復微結構分析測試
藉由SEM觀察自我修復材料微觀裂紋恢復情況,製備寬度為寬度62.32μm的裂紋可於30分鐘內修復0.098μm,與計畫相符(測試結果請參考圖12所示)。
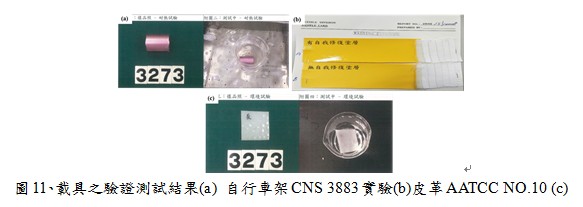
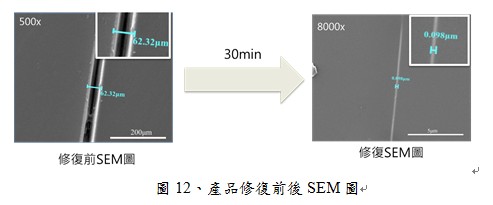
結論
為改變國內傳統業者面臨低價競爭之困境,塑膠中心運用自我修復高分子材料具表面與結構修復運用性廣泛之特點,進行以丙烯酸酯為主之自我修復材料開發,亦成功與業者共同開發出國內首批自製具有表面自我修復功能的自行車架、皮鞋與旅行箱等產品,除有效解決國內自我修復材料仰賴國外進口的問題,同時也將丙烯酸酯單體升級為民生用表面自我修復產品,運用價值大幅提升,由每公斤40元提高約10倍以上價格,擺脫國內業者過去丙烯酸酯材料低價競爭的現況,現在廠商已具備合成自我修復高分子材料之技術與能量,除了運用其特性將產品高值化之外,亦解決國內自我修復材料功能不一問題,並協助業者符合國際新材料發展需求及取得全球市場競爭利基。