塑膠專欄
射出機供料系統節能技術現況分析
3D列印與快速模具
面對全球能源枯竭與溫室氣體排放等問題,國內外橡塑膠加工機械與設備早已朝向節能減碳之方向做研究開發與展示。例如射出機(如圖1所示)之驅動裝置從早期之液壓馬達設計系統,演變成伺服馬達之設計系統等。一部射出機最大耗能系統為射出驅動裝置(約佔整機能耗之50%),其次為射出料管之加熱裝置(約佔整機能耗之20%)。
由於國內伺服馬達系統之關鍵零組件掌握於國外,且國內外已有許多業者競相投入開發與製造生產等因素,間接造成國內橡塑膠機械產業難與國外做競爭。至於在供料系統節能方面,目前仍是以高耗能的電阻式加熱方式為主。因此,本文將介紹改善傳統射出機料管之高耗能問題,探討如何導入節能裝置來降低能耗,達到經濟及環境保護效益。
圖1.塑膠射出機單元示意說明
塑膠射出機之射出料管系統設計:傳統射出料管加熱方式主要採用電阻絲之設計方式做加熱,如圖2所示。然而利用電阻絲做加熱時,因採用接觸式之熱傳導方式,造成射出料管的加熱效率不佳與電阻絲加熱時容易產生燒毀,造成線路開路等問題(如圖3所示)。
電磁感應加熱設計主要依據「電磁感應定律」原理做加熱,如圖4示意所示。亦即由控制系統發出高頻電流(I)至感應線圈,通過被加熱的導體迴路(金屬導管),由於磁通量隨時間發生變化,金屬導管迴路中會產生感應電動勢磁場,利用磁力線與金屬導管內壁圓徑感應,在金屬管管壁產生渦漩電流(Ic),因金屬管電阻小,感應的電動勢磁場便可在金屬管內產生較強的渦漩電流,在被加熱金屬導管內部產生高頻磁場,使被加熱金屬導管內部電子游離出來,多數電子與電子高速碰撞進而產生熱能,使金屬導管自身快速加熱,以達到電磁感應加熱之目的。由於此加熱技術具有熱效高、發熱快、省電節能、安全可靠等諸多優點,解決了傳統利用電阻絲加熱效率低的問題,並已廣泛應用於日常用品,如電磁爐、小型軸承加熱等產品。
近年來,國外射出機製造業者已開始將電磁感應加熱導入到射出機料管之加熱系統,以達到節能與高效率加熱之效益。導入此技術之理由可以從表1之比較表得知,電磁感應加熱相較於電阻式加熱具備相當程度的優勢,在環保節能之全球趨勢發展下,對射出機節能之需求勢必是一項非常有利的節能技術。
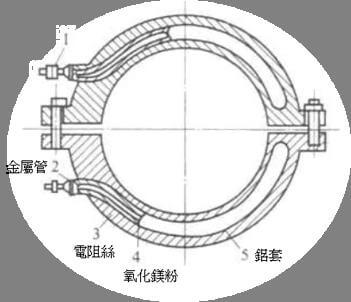
圖2.電阻絲加熱裝置
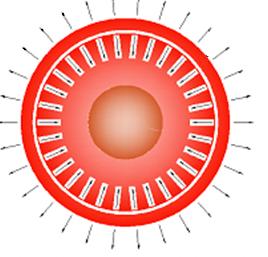
圖3.電阻絲加熱熱源向外散佈
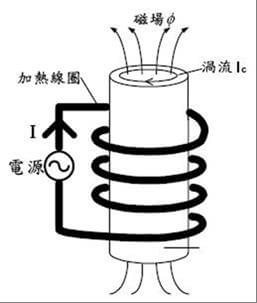
圖4.電磁感應加熱原理說明
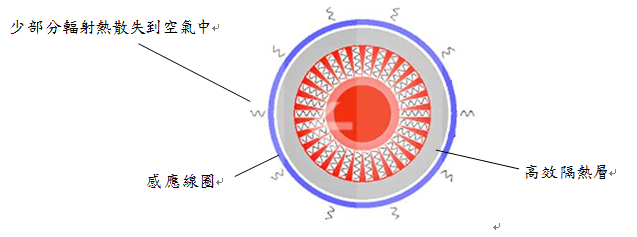
圖5.電磁感應加熱示意說明
表1.利用電阻絲加熱方式與電磁感應加熱方式比較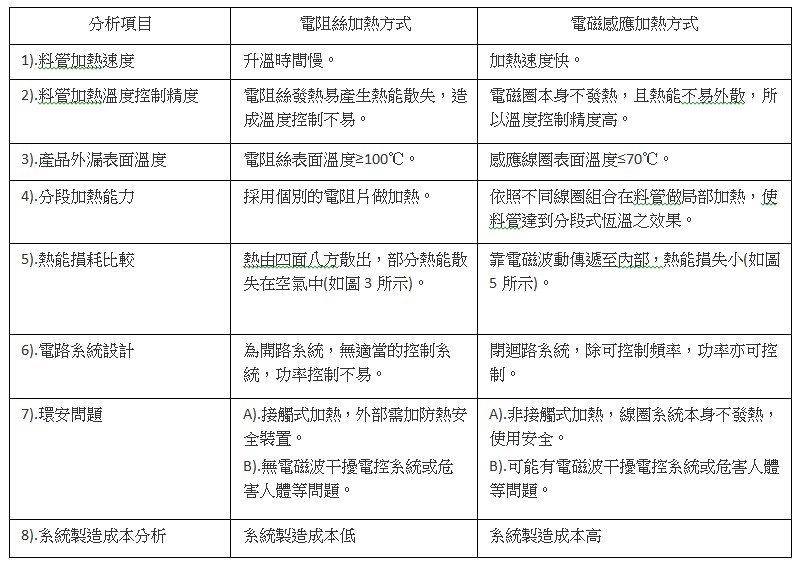
塑膠射出料管利用非接觸式之電磁感應加熱方式取代傳統電阻絲加熱方式,如圖6所示,其商業化競爭優勢在於:
1).耗能約可減少10%~20%以上:一部300頓之油壓馬達射出機,其耗能約為15~20度電/小時;伺服馬達射出機耗能約為6~8度電/小時。因此,塑膠射出機之射出系統導入電磁感應加熱設計後,每部射出機節能效益可達0.5~2.0度電以上/小時。
2).採非接觸傳導加熱方式解決熱量散失等問題,以提升料管加熱效率與加熱速度。
3).料管加熱溫度範圍可均勻分佈,如圖7所示。
4).加熱料管可用隔溫層保護,可降低工安問題產生。
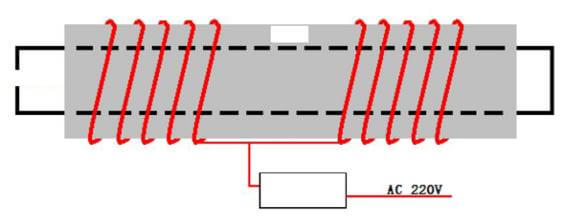
圖6.電磁感應加熱裝置示意圖
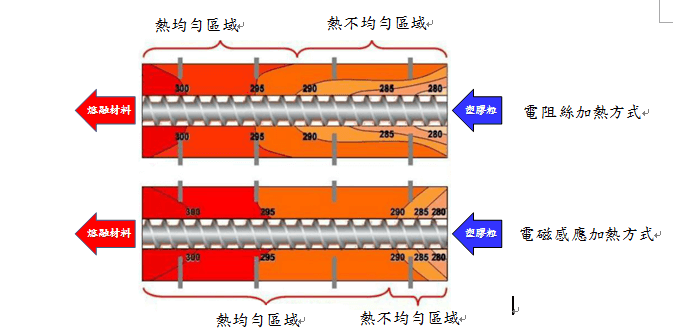
圖7.電磁感應加熱與電阻絲加熱效益分析(註1)
電磁感應加熱雖然具備上述之優勢,但目前尚未普及被應用原因可歸納如下:
1).若料管管徑過大時(如500頓以上之大料管),裝上感應加熱裝置之體積亦較大,因線圈纏繞圈數需多或線圈直徑需加大。
2).使用電磁場原理,易受其他雜波相互干擾,干擾源過大時,影響加熱的穩定性及加熱均勻效果。
3).數位信號控制,控制系統設計繁雜,電子控制零組件價格高昂。
4).感應加熱系統線圈設計不良會導致磁場相互抵銷(如圖8所示),且目前藉由試誤法所累績經驗而來,會耗費人力與物力。
5).線圈互換性不高,一組線圈設計只能對應單一料筒管徑,缺乏通用性(如圖9所示),且形狀複雜工件無法應用(片電阻可以應用在形狀較複雜的工件)。
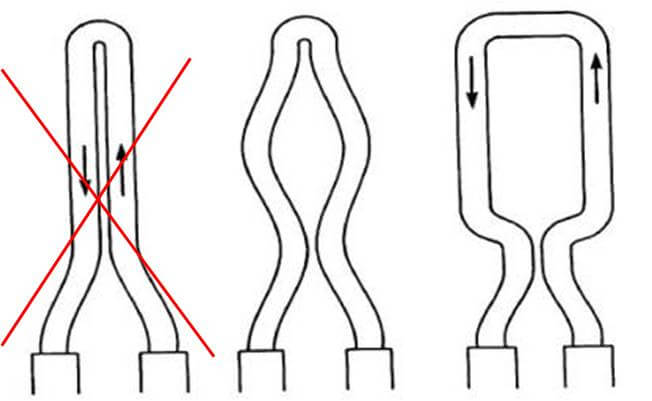
圖8.左,線圈距離太靠近,造成磁場相互抵銷
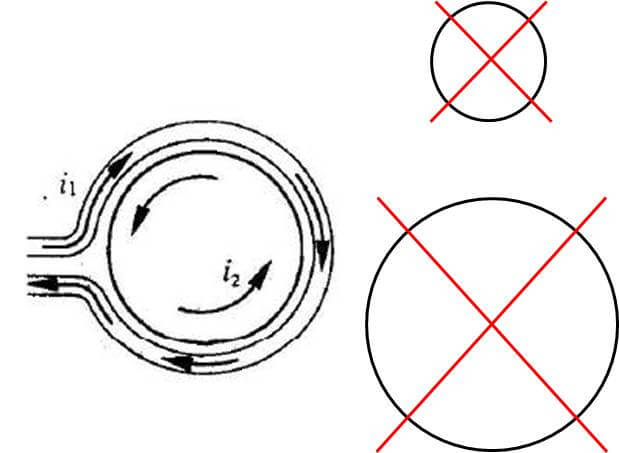
圖9.右,管徑尺寸改變時,線圈無法通用
綜上分析,電磁感應加熱技術導入射出機料管加熱系統之所以未能普及,主要在於感應線圈之設計與製造成本等問題。然而,對節能、減碳與綠色環保等訴求而言,電磁感應加熱方式確實具有相當大的開發價值。因此,財團法人塑膠工業技術發展中心希望以本身長久以來建立的高分子材料、射出成型及機械設計等技術能量,投入電磁感應加熱系統之研發,期能協助業者突破目前的研發瓶頸,開發出更具商業效益之電磁感應加熱射出機供料系統,並將此技術拓展至國內橡塑膠材料加工設備製造業者,如:押出機、吹瓶機…等,協助國內橡塑膠機械設備業者提升在國際上之競爭力。
註1.參考資料來源http://www.xaloy.com/
由於國內伺服馬達系統之關鍵零組件掌握於國外,且國內外已有許多業者競相投入開發與製造生產等因素,間接造成國內橡塑膠機械產業難與國外做競爭。至於在供料系統節能方面,目前仍是以高耗能的電阻式加熱方式為主。因此,本文將介紹改善傳統射出機料管之高耗能問題,探討如何導入節能裝置來降低能耗,達到經濟及環境保護效益。
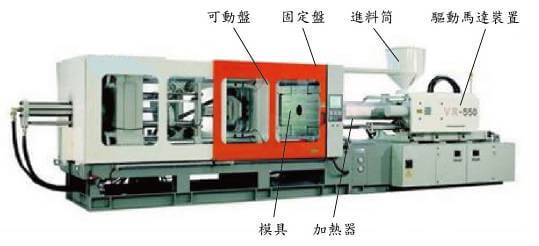
塑膠射出機之射出料管系統設計:傳統射出料管加熱方式主要採用電阻絲之設計方式做加熱,如圖2所示。然而利用電阻絲做加熱時,因採用接觸式之熱傳導方式,造成射出料管的加熱效率不佳與電阻絲加熱時容易產生燒毀,造成線路開路等問題(如圖3所示)。
電磁感應加熱設計主要依據「電磁感應定律」原理做加熱,如圖4示意所示。亦即由控制系統發出高頻電流(I)至感應線圈,通過被加熱的導體迴路(金屬導管),由於磁通量隨時間發生變化,金屬導管迴路中會產生感應電動勢磁場,利用磁力線與金屬導管內壁圓徑感應,在金屬管管壁產生渦漩電流(Ic),因金屬管電阻小,感應的電動勢磁場便可在金屬管內產生較強的渦漩電流,在被加熱金屬導管內部產生高頻磁場,使被加熱金屬導管內部電子游離出來,多數電子與電子高速碰撞進而產生熱能,使金屬導管自身快速加熱,以達到電磁感應加熱之目的。由於此加熱技術具有熱效高、發熱快、省電節能、安全可靠等諸多優點,解決了傳統利用電阻絲加熱效率低的問題,並已廣泛應用於日常用品,如電磁爐、小型軸承加熱等產品。
近年來,國外射出機製造業者已開始將電磁感應加熱導入到射出機料管之加熱系統,以達到節能與高效率加熱之效益。導入此技術之理由可以從表1之比較表得知,電磁感應加熱相較於電阻式加熱具備相當程度的優勢,在環保節能之全球趨勢發展下,對射出機節能之需求勢必是一項非常有利的節能技術。
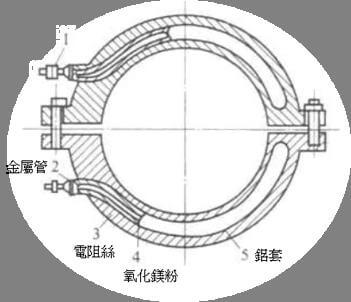
圖2.電阻絲加熱裝置
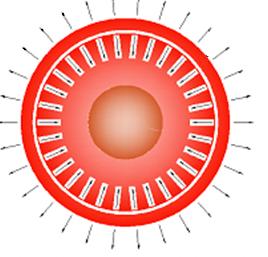
圖3.電阻絲加熱熱源向外散佈
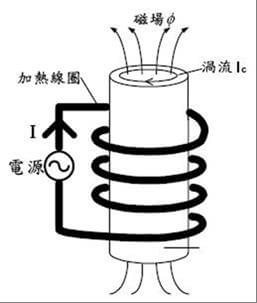
圖4.電磁感應加熱原理說明
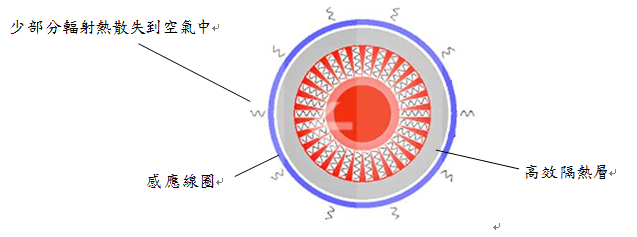
圖5.電磁感應加熱示意說明
表1.利用電阻絲加熱方式與電磁感應加熱方式比較
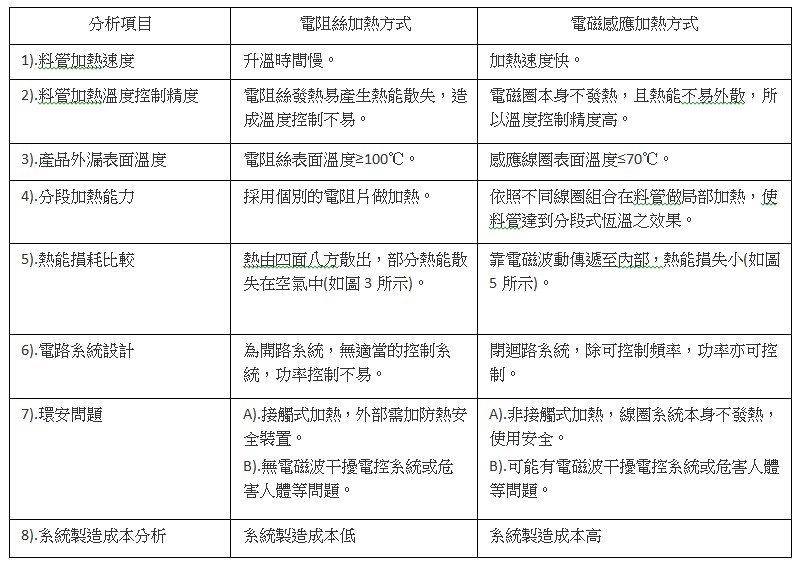
1).耗能約可減少10%~20%以上:一部300頓之油壓馬達射出機,其耗能約為15~20度電/小時;伺服馬達射出機耗能約為6~8度電/小時。因此,塑膠射出機之射出系統導入電磁感應加熱設計後,每部射出機節能效益可達0.5~2.0度電以上/小時。
2).採非接觸傳導加熱方式解決熱量散失等問題,以提升料管加熱效率與加熱速度。
3).料管加熱溫度範圍可均勻分佈,如圖7所示。
4).加熱料管可用隔溫層保護,可降低工安問題產生。
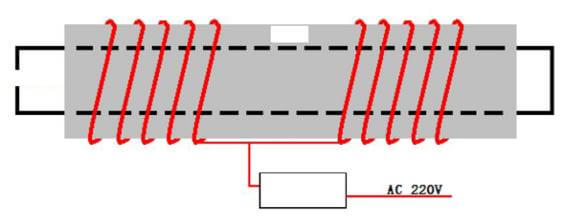
圖6.電磁感應加熱裝置示意圖
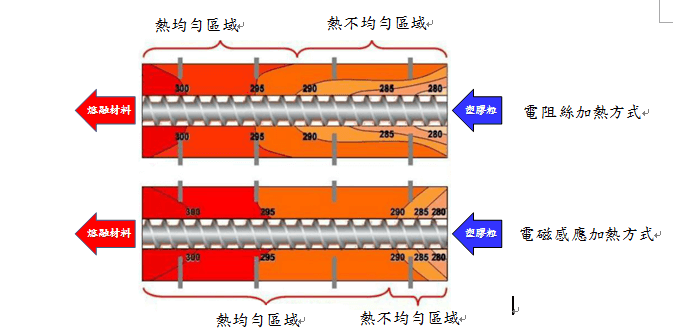
圖7.電磁感應加熱與電阻絲加熱效益分析(註1)
電磁感應加熱雖然具備上述之優勢,但目前尚未普及被應用原因可歸納如下:
1).若料管管徑過大時(如500頓以上之大料管),裝上感應加熱裝置之體積亦較大,因線圈纏繞圈數需多或線圈直徑需加大。
2).使用電磁場原理,易受其他雜波相互干擾,干擾源過大時,影響加熱的穩定性及加熱均勻效果。
3).數位信號控制,控制系統設計繁雜,電子控制零組件價格高昂。
4).感應加熱系統線圈設計不良會導致磁場相互抵銷(如圖8所示),且目前藉由試誤法所累績經驗而來,會耗費人力與物力。
5).線圈互換性不高,一組線圈設計只能對應單一料筒管徑,缺乏通用性(如圖9所示),且形狀複雜工件無法應用(片電阻可以應用在形狀較複雜的工件)。
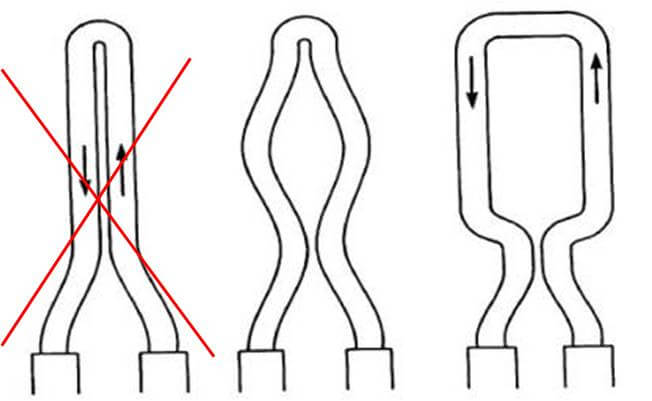
圖8.左,線圈距離太靠近,造成磁場相互抵銷
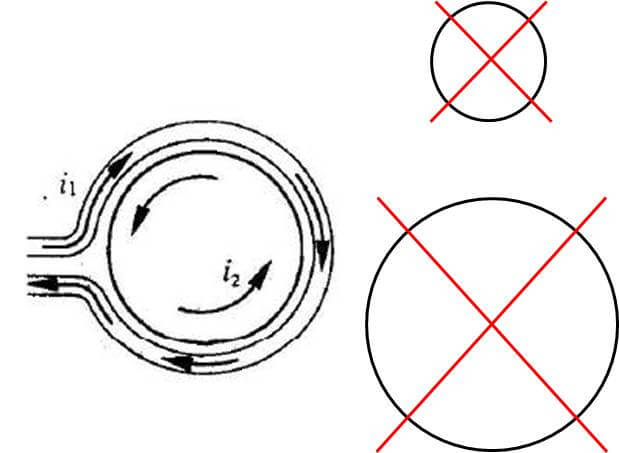
圖9.右,管徑尺寸改變時,線圈無法通用
綜上分析,電磁感應加熱技術導入射出機料管加熱系統之所以未能普及,主要在於感應線圈之設計與製造成本等問題。然而,對節能、減碳與綠色環保等訴求而言,電磁感應加熱方式確實具有相當大的開發價值。因此,財團法人塑膠工業技術發展中心希望以本身長久以來建立的高分子材料、射出成型及機械設計等技術能量,投入電磁感應加熱系統之研發,期能協助業者突破目前的研發瓶頸,開發出更具商業效益之電磁感應加熱射出機供料系統,並將此技術拓展至國內橡塑膠材料加工設備製造業者,如:押出機、吹瓶機…等,協助國內橡塑膠機械設備業者提升在國際上之競爭力。
註1.參考資料來源http://www.xaloy.com/