塑膠專欄
產品開發的捷徑—從快速原型至快速模具之快速試製技術
3D列印與快速模具
一、前言
隨著社會經濟結構變化、科技發展一日千里,市場需求變化快速使得產品生命週期加速縮短,這種趨勢在汽車、機車、電子產品、家電產品、玩具等製造業尤其顯著,10 年前開發一輛新汽車的時間大約為60 個月,現在僅18 個月;而HP(惠普)公司有80%以上的利潤來自不滿2年的新產品。產品上市後隨時可能被新產品取代,如何有效縮短新產品的研發週期,加速符合市場需求及潮流之新產品上市時間以提升競爭優勢,成為產業面臨的一大挑戰,亦為製造業致勝的關鍵。快速試製(Rapid Manufacturing, RM)就是在這種背景下逐步成形與發展,而其中之關鍵技術主要包括快速原型(Rapid Prototyping, RP)與快速模具(Rapid Tooling, RT)技術。
二、快速原型技術
3D列印是近年來工業上最夯的話題,3D列印技術為快速原型技術之一,而所謂RP技術顧名思義是一種在短時間內即能製作出所需要原型的技術。快速原型技術是80年代發展起來的一種新型製造技術,與傳統的切削加工不同,RP採用逐層材料累加的方式進行實體模型的製做。自1987年美國3D SYSTEMS公司首先公開液態製造亦被稱為光造形法(Stereo Lithography Apparatus, SLA)的系統以來,許多先進國家陸續開發出各式各樣的RP系統,當今主要之RP技術分類如圖1所示。RP的用途主要是設計可視化、設計驗證與檢討、功能測試等,在新產品開發過程中,RP能使產品得到最佳化設計並縮短產品開發週期,降低開發成本。
RP雖然擁有許多新產品開發的技術優勢,但比起RP,產業更需要快速模具技術(Rapid Tooling,RT)!尤其是對於製造產業來說,RP的材料限制多且種類少、不能規模化量產、成本高昂等瓶頸,使其難以成為產線應用的主流製造技術。在 1997 年的RP 研討會中,多位發表人一再強調「勿止於RP」(Do not stop after prototype),意即強調後續快速模具(Rapid Tooling, RT)製程之重要性。
圖1RP系統分類(資料來源:塑膠中心整理)
三、快速模具技術(Rapid Tooling, RT)
快速模具(RT)簡單的說就是利用快速原型(RP) 直接或間接的快速製造出可進行少量生產或試產的模具。有了RT技術,產品可快速的被製造出來,達到快速製造的目的,使得RP 在研發階段的利益,直接延伸到生產階段的利益,圖2為RT的種類與可應用範圍。RT的製作大致可分為直接造模法及間接造模法。所謂直接造模法就是在RP加工時其加工的外型就是模具;而間接造模法則是在RP 階段時其外型就是一個我們想要得到的產品,之後再經過翻製以得到模具。直接造模法多由粉末類快速原型系統直接製出公、母模具,其成形特性為利用掃瞄式CO2雷射,掃瞄欲成形部分的粉末,使其互相結合,利用積層造形的方法直接生產能承受較高負荷的金屬材料工件或量產用的模具。例如DTM公司的Rapid Tool、EOS公司的DMLS、Extrude Home公司的ProMetal…等。其中以DTM公司的SLS製程最具代表,其原理為利用特製金屬粉末,由SLS快速原型系統直接將公、母模個別製造出來,成品稱為“粗胚(Green Part)”,然後將粗胚放入火爐 (Furnace)將黏結劑 (binder)融出,所得到的成品稱為“Brown Part”,最後將Brown Part在高溫爐中滲銅,待其冷卻凝固後,即可得高密度模具。間接造模法是利用RP來翻製(Duplicate)模具,間接造魔法的技術包括矽膠模(RTV Silicone Rubber Mould)、精密鑄造(Investment Casting)、樹脂型模具(Resin based Mold)、金屬噴塗模(Metal Spraying)、3D System(KelTool)及CEMCOM公司(NCC Tooling)…等。
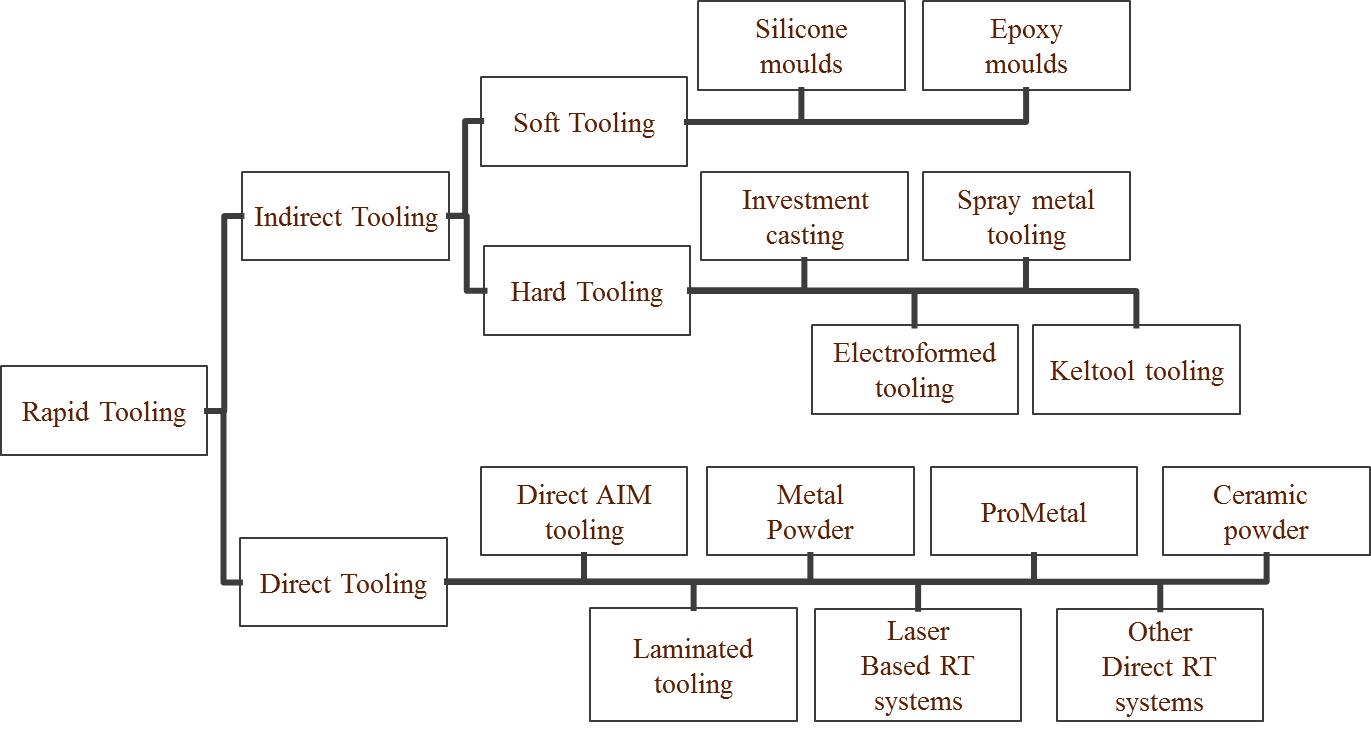
圖2快速模具的種類與應用(資料來源:塑膠中心整理)
快速模具技術相對於傳統模具之最大優點在於開發成本低、時間短,但直接造模法所使用的設備與材料成本相當而貴,動則需耗費新台幣上千萬元,因此在國內並不普及,僅止於學術單位或研究單位做為研究上之使用。目前國內開發用快速模具以矽膠模(Silicone Mold)為主,而生產件數約十件左右,且材料種類及強度均受限,若要開發百件以上塑膠產品,將耗時數月且所費不貲,非常不符經濟效益。屬於間接造模法的樹脂型快速模具,主要優勢是可應用在塑膠射出成型模具,依各家開發的樹脂材料特性之不同,所製做的模具可達到數十至數百模次,甚至是上千模次的使用量,足以滿足業者小批量產的需求。
四、應用實例-樹脂型快速模具應用於塑膠製品之快速試製
本案例將以迴紋針收集盒為設計,利用快速試製技術,產出最終實體產品。其中RT利用間接造模法之樹脂型快速模具技術來製做,公、母模之母型(Master Pattern)製做所使用的是SLA的RP系統。翻模材料為環氧樹脂並添加無機物填充粉體,以改善樹脂型快速模具的機械性質,提高模具使用模次。圖3為樹脂型快速模具之製做流程。
圖3快速模具製做程序
製做流程說明:
1. 數據模型:設計一款迴紋針收集盒為模型,應用3D 繪圖軟體完成產品設計,確認產品外形及尺寸(如圖4所示)。
2. 將3D設計圖轉換成STL檔讀入RP系統,製做公母模仁之Master Pattern(圖5)。
3. 模仁翻製:將公母模仁之Master Pattern定位於模框中,進行模仁灌注前,灌注材料需於真空室先行除泡,於灌注後再放至真空室脫泡一次。後依環氧樹脂硬化條件於室溫或烤箱進行硬化製程。最後待硬化完成後將Master Pattern取出,完成模仁翻製。
4. 模具組裝:模具組裝工程包括翻製後模仁背面多餘樹脂機製銑平,鑽頂出銷孔並安裝頂出銷,合模與修模(圖6),最後將固定模板、可動模板、導銷、澆口等部份組合成射出成型模具(圖7)。
5. 射出成型及測試:本次射出成型材料是以熱塑性塑膠(Thermoplastics)聚丙烯(Polypropylene, PP)為主,以Toshiba IS220射出成型機進行射出成型測試,射出溫度約為180℃。圖8為射出成型所得之迴紋針收集盒製品。
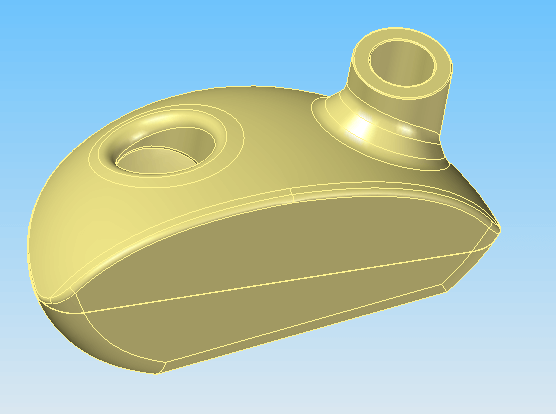
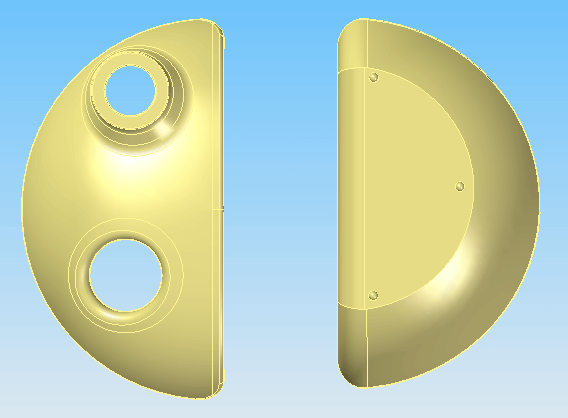
圖4迴紋針收集盒數據模型
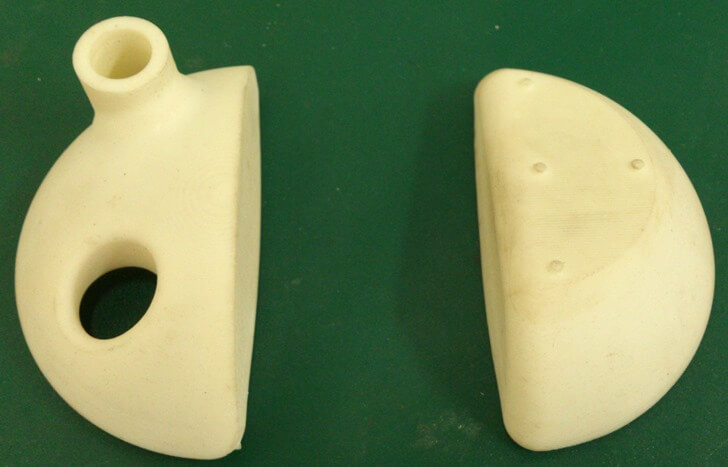
圖5SLA系統RP-迴紋針收集盒母型(Master pattern)
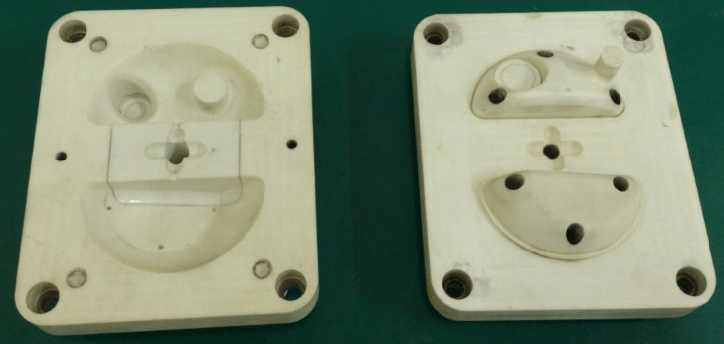
圖6樹脂型快速模具-迴紋針收集盒快速模具外觀
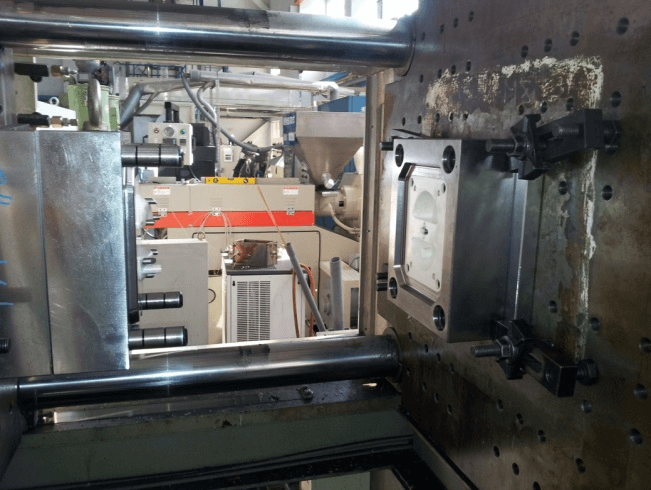
圖7迴紋針收集盒模仁組裝至模座並鎖付至射出成型機之情形
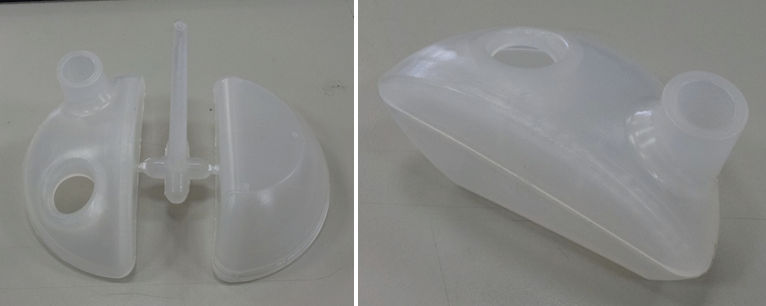
圖8射出成型速品-迴紋針盒
四、結論
傳統的模具製做時間通常需要1~3個月,若遇到較複雜的模具,加工的時間亦會增加,再加上模具修模時間,於製模的時間與成本將耗費更多。相較於RT,本案例迴紋針收集盒從RP的製做到RT的製做只需要7個工作天,並可事先以RP做為開發產品確認,大幅降低開模的時間,從RP到RT的快速試製程序,可讓開發者在同步工程下,掌握整個設計與製做與生產流程,達到縮短製造時間即趕善傳統製程的目的。另外,本案例採用樹脂型快速模具應用於射出成型加工製程,在試量產100模後,模具仍保存良好,顯示利用樹脂型快速模具的確可達到小試量產的目的。再加上快速模具技術具有製模週期短、工藝簡單、製模成本低、能滿足特定產品功能需求等顯著優點,特別適用於新產品開發快速試製、工藝驗證、功能驗證以及多樣式小批量生產,讓業者能在有限的時間與資源內創造產品更大的優勢與競爭力。
參考文獻
[1] 林英傑,“產品開發的新利器-RP/RT技術”,模具技術資訊,1頁-10頁,9月,1997年。
[2] 陳復東,“射出成型用之快速模具實驗探討”,國立臺灣大學機械工程學研究所論文,1999年。
[3] 汪家昌、鄭正元,“快速原型技術至快速模具技術之發展”,經濟部技術處,1999模具技術成果暨論文集,台北市世貿大樓展覽館一樓,207頁-212頁,8月,1999年。
[4] 安超群、邱家祥、劉永隆,“快速模具在塑膠射出之應用”,經濟部技術處,1999模具技術成果暨論文集,台北市世貿大樓展覽館一樓,231頁-232頁,8月,199年。
[5] 孟繼洛、傅兆章、許源泉、黃聖芳、李炳寅,“快速成形及快速模具技術”,機械製造,第十一章,全華圖書,6月,2005年。
[6] 鄧至均,“奈米碳材/環氧樹脂複合材料之製備與導熱性質研究”,國立清華大學化學工程學系論文摘要,I頁,2010年。
隨著社會經濟結構變化、科技發展一日千里,市場需求變化快速使得產品生命週期加速縮短,這種趨勢在汽車、機車、電子產品、家電產品、玩具等製造業尤其顯著,10 年前開發一輛新汽車的時間大約為60 個月,現在僅18 個月;而HP(惠普)公司有80%以上的利潤來自不滿2年的新產品。產品上市後隨時可能被新產品取代,如何有效縮短新產品的研發週期,加速符合市場需求及潮流之新產品上市時間以提升競爭優勢,成為產業面臨的一大挑戰,亦為製造業致勝的關鍵。快速試製(Rapid Manufacturing, RM)就是在這種背景下逐步成形與發展,而其中之關鍵技術主要包括快速原型(Rapid Prototyping, RP)與快速模具(Rapid Tooling, RT)技術。
二、快速原型技術
3D列印是近年來工業上最夯的話題,3D列印技術為快速原型技術之一,而所謂RP技術顧名思義是一種在短時間內即能製作出所需要原型的技術。快速原型技術是80年代發展起來的一種新型製造技術,與傳統的切削加工不同,RP採用逐層材料累加的方式進行實體模型的製做。自1987年美國3D SYSTEMS公司首先公開液態製造亦被稱為光造形法(Stereo Lithography Apparatus, SLA)的系統以來,許多先進國家陸續開發出各式各樣的RP系統,當今主要之RP技術分類如圖1所示。RP的用途主要是設計可視化、設計驗證與檢討、功能測試等,在新產品開發過程中,RP能使產品得到最佳化設計並縮短產品開發週期,降低開發成本。
RP雖然擁有許多新產品開發的技術優勢,但比起RP,產業更需要快速模具技術(Rapid Tooling,RT)!尤其是對於製造產業來說,RP的材料限制多且種類少、不能規模化量產、成本高昂等瓶頸,使其難以成為產線應用的主流製造技術。在 1997 年的RP 研討會中,多位發表人一再強調「勿止於RP」(Do not stop after prototype),意即強調後續快速模具(Rapid Tooling, RT)製程之重要性。
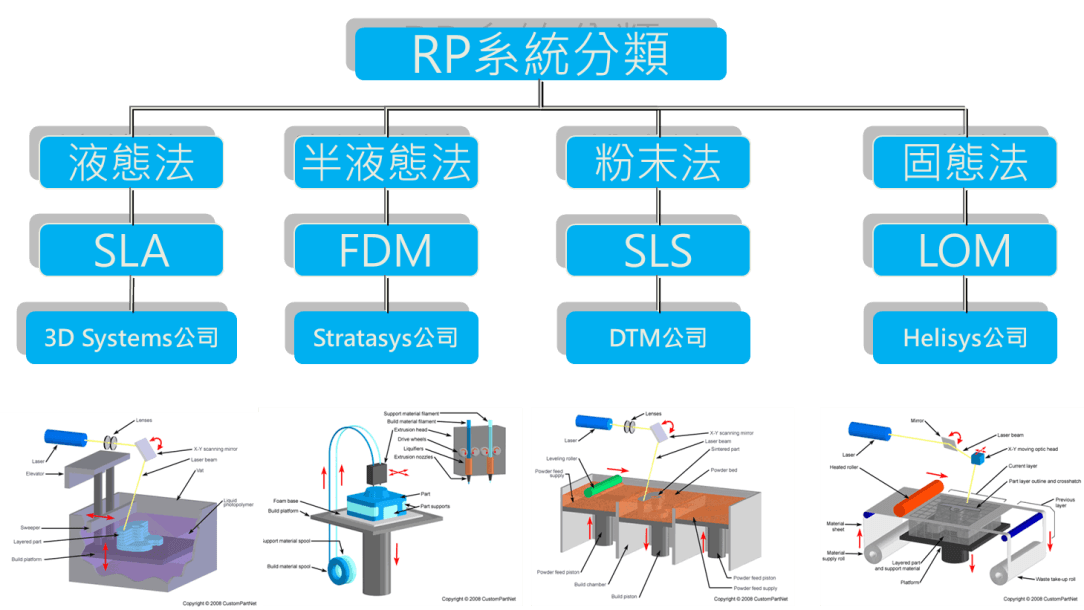
三、快速模具技術(Rapid Tooling, RT)
快速模具(RT)簡單的說就是利用快速原型(RP) 直接或間接的快速製造出可進行少量生產或試產的模具。有了RT技術,產品可快速的被製造出來,達到快速製造的目的,使得RP 在研發階段的利益,直接延伸到生產階段的利益,圖2為RT的種類與可應用範圍。RT的製作大致可分為直接造模法及間接造模法。所謂直接造模法就是在RP加工時其加工的外型就是模具;而間接造模法則是在RP 階段時其外型就是一個我們想要得到的產品,之後再經過翻製以得到模具。直接造模法多由粉末類快速原型系統直接製出公、母模具,其成形特性為利用掃瞄式CO2雷射,掃瞄欲成形部分的粉末,使其互相結合,利用積層造形的方法直接生產能承受較高負荷的金屬材料工件或量產用的模具。例如DTM公司的Rapid Tool、EOS公司的DMLS、Extrude Home公司的ProMetal…等。其中以DTM公司的SLS製程最具代表,其原理為利用特製金屬粉末,由SLS快速原型系統直接將公、母模個別製造出來,成品稱為“粗胚(Green Part)”,然後將粗胚放入火爐 (Furnace)將黏結劑 (binder)融出,所得到的成品稱為“Brown Part”,最後將Brown Part在高溫爐中滲銅,待其冷卻凝固後,即可得高密度模具。間接造模法是利用RP來翻製(Duplicate)模具,間接造魔法的技術包括矽膠模(RTV Silicone Rubber Mould)、精密鑄造(Investment Casting)、樹脂型模具(Resin based Mold)、金屬噴塗模(Metal Spraying)、3D System(KelTool)及CEMCOM公司(NCC Tooling)…等。
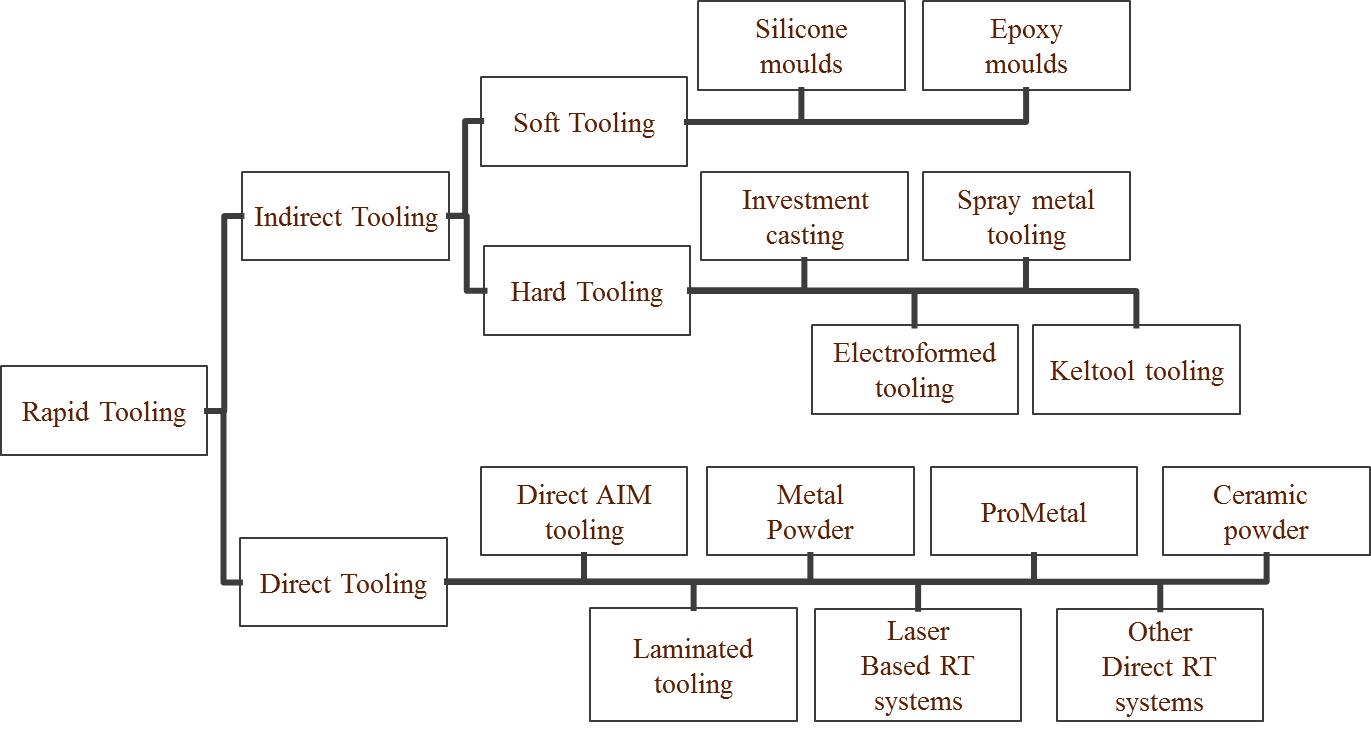
圖2快速模具的種類與應用(資料來源:塑膠中心整理)
快速模具技術相對於傳統模具之最大優點在於開發成本低、時間短,但直接造模法所使用的設備與材料成本相當而貴,動則需耗費新台幣上千萬元,因此在國內並不普及,僅止於學術單位或研究單位做為研究上之使用。目前國內開發用快速模具以矽膠模(Silicone Mold)為主,而生產件數約十件左右,且材料種類及強度均受限,若要開發百件以上塑膠產品,將耗時數月且所費不貲,非常不符經濟效益。屬於間接造模法的樹脂型快速模具,主要優勢是可應用在塑膠射出成型模具,依各家開發的樹脂材料特性之不同,所製做的模具可達到數十至數百模次,甚至是上千模次的使用量,足以滿足業者小批量產的需求。
四、應用實例-樹脂型快速模具應用於塑膠製品之快速試製
本案例將以迴紋針收集盒為設計,利用快速試製技術,產出最終實體產品。其中RT利用間接造模法之樹脂型快速模具技術來製做,公、母模之母型(Master Pattern)製做所使用的是SLA的RP系統。翻模材料為環氧樹脂並添加無機物填充粉體,以改善樹脂型快速模具的機械性質,提高模具使用模次。圖3為樹脂型快速模具之製做流程。
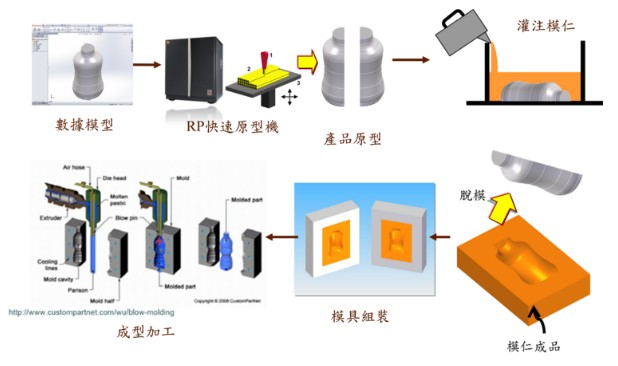
製做流程說明:
1. 數據模型:設計一款迴紋針收集盒為模型,應用3D 繪圖軟體完成產品設計,確認產品外形及尺寸(如圖4所示)。
2. 將3D設計圖轉換成STL檔讀入RP系統,製做公母模仁之Master Pattern(圖5)。
3. 模仁翻製:將公母模仁之Master Pattern定位於模框中,進行模仁灌注前,灌注材料需於真空室先行除泡,於灌注後再放至真空室脫泡一次。後依環氧樹脂硬化條件於室溫或烤箱進行硬化製程。最後待硬化完成後將Master Pattern取出,完成模仁翻製。
4. 模具組裝:模具組裝工程包括翻製後模仁背面多餘樹脂機製銑平,鑽頂出銷孔並安裝頂出銷,合模與修模(圖6),最後將固定模板、可動模板、導銷、澆口等部份組合成射出成型模具(圖7)。
5. 射出成型及測試:本次射出成型材料是以熱塑性塑膠(Thermoplastics)聚丙烯(Polypropylene, PP)為主,以Toshiba IS220射出成型機進行射出成型測試,射出溫度約為180℃。圖8為射出成型所得之迴紋針收集盒製品。
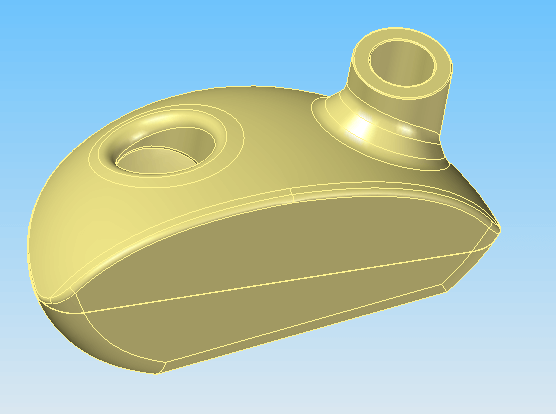
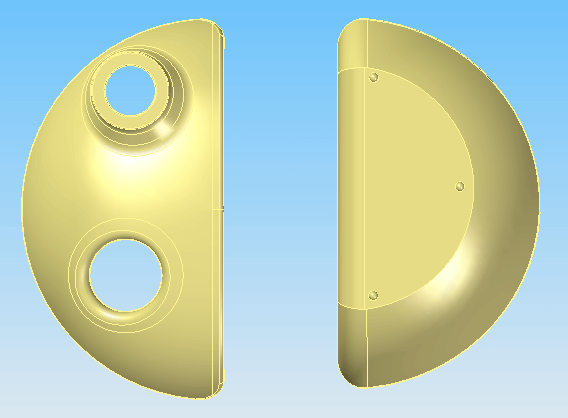
圖4迴紋針收集盒數據模型
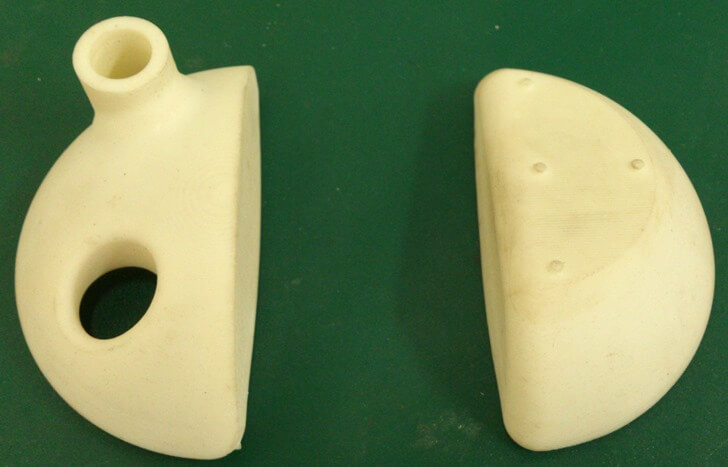
圖5SLA系統RP-迴紋針收集盒母型(Master pattern)
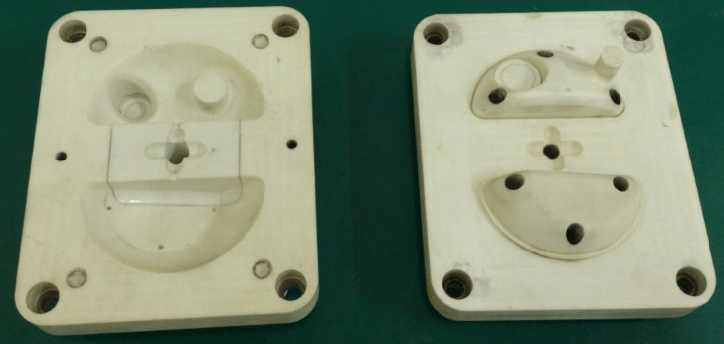
圖6樹脂型快速模具-迴紋針收集盒快速模具外觀
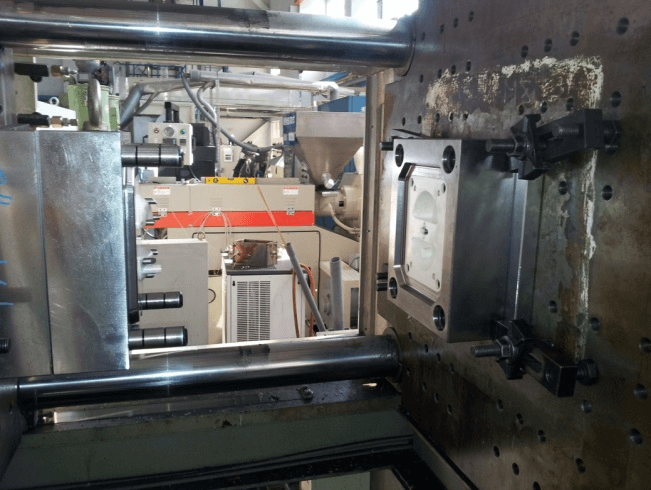
圖7迴紋針收集盒模仁組裝至模座並鎖付至射出成型機之情形
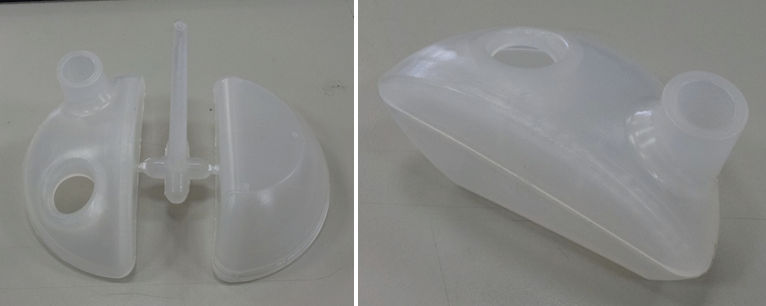
圖8射出成型速品-迴紋針盒
四、結論
傳統的模具製做時間通常需要1~3個月,若遇到較複雜的模具,加工的時間亦會增加,再加上模具修模時間,於製模的時間與成本將耗費更多。相較於RT,本案例迴紋針收集盒從RP的製做到RT的製做只需要7個工作天,並可事先以RP做為開發產品確認,大幅降低開模的時間,從RP到RT的快速試製程序,可讓開發者在同步工程下,掌握整個設計與製做與生產流程,達到縮短製造時間即趕善傳統製程的目的。另外,本案例採用樹脂型快速模具應用於射出成型加工製程,在試量產100模後,模具仍保存良好,顯示利用樹脂型快速模具的確可達到小試量產的目的。再加上快速模具技術具有製模週期短、工藝簡單、製模成本低、能滿足特定產品功能需求等顯著優點,特別適用於新產品開發快速試製、工藝驗證、功能驗證以及多樣式小批量生產,讓業者能在有限的時間與資源內創造產品更大的優勢與競爭力。
參考文獻
[1] 林英傑,“產品開發的新利器-RP/RT技術”,模具技術資訊,1頁-10頁,9月,1997年。
[2] 陳復東,“射出成型用之快速模具實驗探討”,國立臺灣大學機械工程學研究所論文,1999年。
[3] 汪家昌、鄭正元,“快速原型技術至快速模具技術之發展”,經濟部技術處,1999模具技術成果暨論文集,台北市世貿大樓展覽館一樓,207頁-212頁,8月,1999年。
[4] 安超群、邱家祥、劉永隆,“快速模具在塑膠射出之應用”,經濟部技術處,1999模具技術成果暨論文集,台北市世貿大樓展覽館一樓,231頁-232頁,8月,199年。
[5] 孟繼洛、傅兆章、許源泉、黃聖芳、李炳寅,“快速成形及快速模具技術”,機械製造,第十一章,全華圖書,6月,2005年。
[6] 鄧至均,“奈米碳材/環氧樹脂複合材料之製備與導熱性質研究”,國立清華大學化學工程學系論文摘要,I頁,2010年。